Generación de Vapor
Los generadores de vapor son un componente básico en todo tipo de procesos industriales y la elección del mejor sistema es clave para garantizar la adecuada eficiencia energética del sistema y el abastecimiento de vapor en las condiciones requeridas. El vapor industrial se obtiene a través de generadores que ejecutan procesos de calentamiento para vaporizar agua a alta presión, vapor que puede ser recalentado o simplemente saturado según la aplicación que se le quiera dar
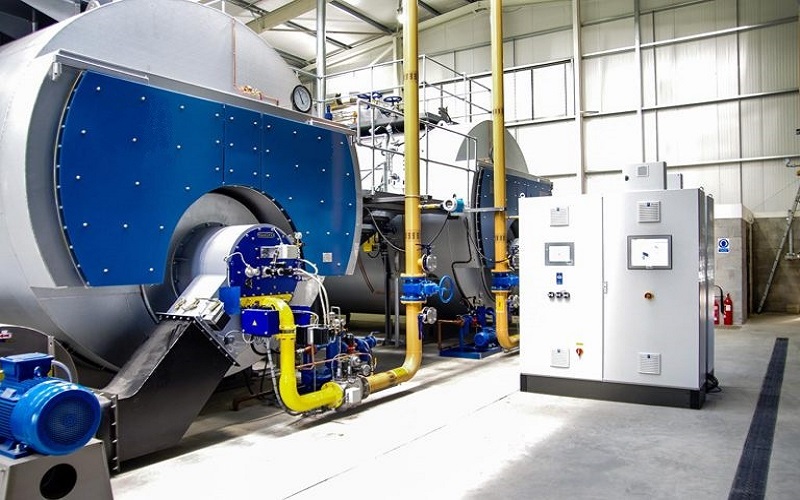
Las calderas de vapor son calderas especialmente diseñadas para trabajar en instalaciones donde se necesite una gran transferencia de energía calorífica, como son procesos industriales, estas calderas tienen como fluido caloportador el agua que lo convierten en vapor y se pueden clasificar según la disposición de los fluidos en: calderas de tubos de agua o acuotubulares y calderas de tubos de humos o piro tubulares.
“Hay mucho interés por parte de la industria en reducir su facturación de energía y aunque el vapor no es el único generador, es uno de las más importantes para lograr éste objetivo.”
Enfoque
Nuestros conocimientos van desde los básicos del vapor, su utilización y componentes de la instalación, con lo que estamos capacitados para ofrecer un rediseño, montaje, operación y mantenimiento y así se puedan obtener mejoras en la producción, seguridad y eficiencia energética. Además nos enfocamos en:
- Mejores prácticas para reducir los costes.
- Mantenimiento de instalaciones de vapor.
- Recuperación de Condensado.
- Mejoras en eficiencia y productividad.
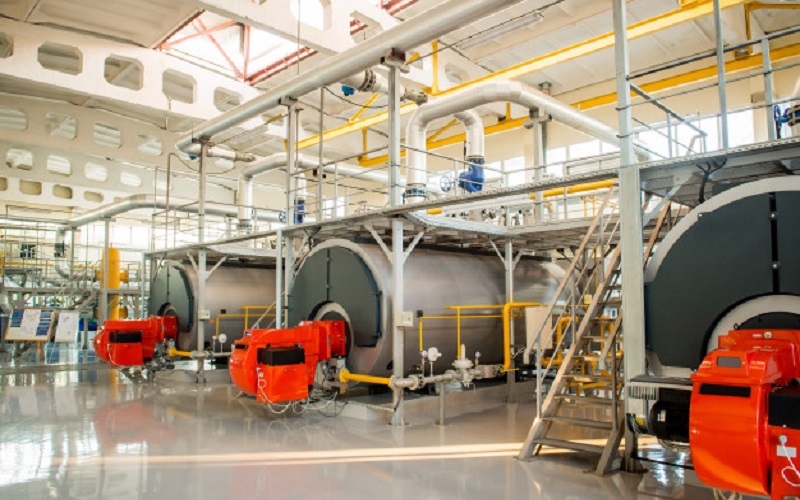
Como minimizar los costes de vapor
Una de las formas de minimizar los costes de vapor es contar con tecnologías para incrementar la vida útil de la caldera en plantas industriales, entre las que se mencionan un controlador de demanda de vapor, que no es más que un sistema de control que garantiza la llegada del combustible al quemador de los generadores de vapor con la presión y temperatura requerida.
La segunda de las formas de minimizar los costes de vapor es modernizar o modificar los quemadores de las calderas o los sistemas de combustión para encender combustibles múltiples. Algunas plantas generan rechazos o subproductos inutilizables y no comercializables, sin embargo, vale la pena hacer el esfuerzo de invertir en modificaciones múltiples de sistemas de calderas de combustible que serán rentables.
Los procesos que dependen críticamente del calentamiento con vapor deben tener una eliminación confiable del condensado. El respaldo de condensado dentro del equipo de transferencia de calor (debido a un bloqueo, una contrapresión excesiva en los problemas de la tubería de retorno o un golpe de ariete) se debe drenar para evitar las interrupciones en el calentamiento del vapor.
Entretanto, la tercera de las formas de minimizar los costes de vapor es evaluar que el dimensionamiento de la tubería de retorno de condensado sea adecuado. La provisión de una separación adecuada del condensado de vapor es un requisito esencial dentro de un sistema de vapor y esto, muchas veces, cambia cuando se conectan más fuentes de condensado, o cuando se produce una generación excesiva de vapor repentino en la tubería de retorno por cambios operacionales del equipo.
La última de las formas de minimizar los costes de vapor en una planta, pero no la menos importante, es explorar la generación de vapor de calor residual de los incineradores o calentadores que expulsan los gases de combustión a pilas a temperaturas superiores a 200 ºC. La mayoría de las plantas tienen incineradores de gas residual que operan continuamente para quemar gases tóxicos y otros gases residuales del proceso.
Debido a que estos flujos de gas residual se producen ocasionalmente y en su mayoría en pequeñas cantidades, el combustible siempre dispara los lechos del incinerador para mantener la temperatura de incineración. En algunas plantas, esta combustión de combustible casi equivale al consumo de una caldera de tamaño pequeño o mediano.